Inventory Management: The Challenge
Today, a good number of retailers use automated procurement systems to supply their stores. However, this process is often sub-optimal for a variety of reasons, often leading to inaccurate or incomplete inventory data. Consequently, many retailers struggle with under- or over-stocking certain products, resulting in potential lost sales or the risk of unsold inventory (tied up capital).
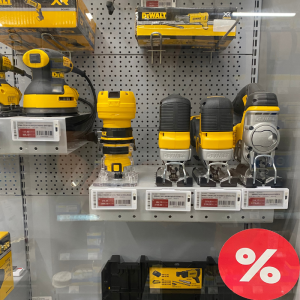
Solution
The Pricer electronic shelf label system offers valuable support to a number of strategies that can be used to maintain accurate inventory levels. The initial approach involves simplifying the identification of questionable inventory by highlighting products with low or negative inventory. For example, the above can be configured in such a way that, before the opening of the store, the digital labels (ESL) associated with the products showing a low level of stock are “illuminated”. Labels change the display to “employee mode”, i.e. they display information such as stock status, how much quantity is arriving, delivery date, etc.
Also, it is possible to carry out a targeted inspection of specific products during the day, where employees are guided to a group of products for inspection via the “Flash” option and a mapped display of the store. The value of both options is time savings and more precise information.
An additional effective method is the system of filling the shelves with goods using the “Flash” option, that is, matching the product that the employee is holding in his hand with the product on the shelf. With this method, we significantly reduce errors when replenishing goods: we avoid a common mistake such as placing a product in front of a visually similar, but not identical, item – we cover up the entire row, which certainly leads to subsequent errors…
Take for example the following:
- the new employee is a foreign citizen without good knowledge of the language
- in the first working week, he was given the task of replenishing the shelves with pasta
- the employee is not familiar with the offer, and the types of pasta all look the same
By scanning the product, the flash on the label corresponding to the barcode will light up, and the employee can safely replenish the goods. With this, the new employee can be as efficient as a “more experienced” employee in a very short period.
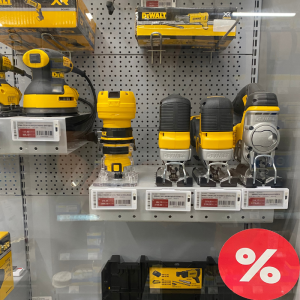
Inventory Management: The Challenge
Today, a good number of retailers use automated procurement systems to supply their stores. However, this process is often sub-optimal for a variety of reasons, often leading to inaccurate or incomplete inventory data. Consequently, many retailers struggle with under- or over-stocking certain products, resulting in potential lost sales or the risk of unsold inventory (tied up capital).
Solution
The Pricer electronic shelf label system offers valuable support to a number of strategies that can be used to maintain accurate inventory levels. The initial approach involves simplifying the identification of questionable inventory by highlighting products with low or negative inventory. For example, the above can be configured in such a way that, before the opening of the store, the digital labels (ESL) associated with the products showing a low level of stock are “illuminated”. Labels change the display to “employee mode”, i.e. they display information such as stock status, how much quantity is arriving, delivery date, etc.
Also, it is possible to carry out a targeted inspection of specific products during the day, where employees are guided to a group of products for inspection via the “Flash” option and a mapped display of the store. The value of both options is time savings and more precise information.
An additional effective method is the system of filling the shelves with goods using the “Flash” option, that is, matching the product that the employee is holding in his hand with the product on the shelf. With this method, we significantly reduce errors when replenishing goods: we avoid a common mistake such as placing a product in front of a visually similar, but not identical, item – we cover up the entire row, which certainly leads to subsequent errors…
Take for example the following:
- the new employee is a foreign citizen without good knowledge of the language
- in the first working week, he was given the task of replenishing the shelves with pasta
- the employee is not familiar with the offer, and the types of pasta all look the same
By scanning the product, the flash on the label corresponding to the barcode will light up, and the employee can safely replenish the goods. With this, the new employee can be as efficient as a “more experienced” employee in a very short period.
Social Media